Plate Heat Exchangers
Your Chief Benefit—High Efficiency with Life Cycle Support
Tranter is soon entering its fifth decade engineering, manufacturing and supporting gasketed plate heat exchangers. We have listened carefully to our customers. Beyond simply purchasing a plate heat exchanger that meets a spec, customers tell us they want an added-value solution with maintenance-friendly designs and life cycle support. We have responded with significant investments in global coverage with a local presence. We are committed to extending our support to you through our specialized Service Center network, with preventive maintenance services and emergency uptime restoration service devoted solely to plate-type heat exchangers.
Modularity For Flexibility
The Tranter Plate Heat Exchanger provides outstanding efficiency transferring heat from one liquid to another or from steam to liquid. This modular exchanger combines frames, plates and connections to form a variety of configurations. By using different types of plates, with different characteristics, the exchangers can be adapted to a wide variety of applications. The exchangers can easily be disassembled for inspection, maintenance or even expansion by adding plates.
High Heat Transfer Rates
The flow turbulence created by Tranter Plate Heat Exchangers promotes maximum heat transfer. With their high efficiency, the exchangers can handle temperature approaches of less than 1°C (2°F). The unit also offers “U” or “K “ values 3 to 6 times higher than shell & tube exchangers.
Tranter is a market leader in the development of high-efficiency plate pattern designs and flow configurations. Among these are Ultraflex plate patterns, our unique, neutral-plane gasket groove design and the ability to configure our units in either a parallel or a diagonal flow configuration. These options improve the utilization of available pressure drops and increase the efficiency of our units. Our diagonal flow option is especially important on larger flows and low NTU duties.
Compact Design
With its high efficiency, the Tranter Plate Heat Exchanger conserves footprint and floor loading far beyond what is possible with an identical duty shell & tube heat exchanger. A Tranter Plate Heat Exchanger can fit into 20–50% of a shell & tube footprint including service and maintenance space. This compact footprint makes productive use of tight spaces, especially important with production expansions. Lighter weight makes transportation and rigging less costly. And, it costs less.
Self-Cleaning Action
The unit’s velocity profile and induced turbulence causes dirty product deposits to be continually removed from the heat transfer surface during operation, thereby reducing fouling. The plate turbulence also enhances the effectiveness of water backflushing and cleaning in place (CIP) procedures with less frequent need to disassemble the exchanger. Plates can be electropolished to make cleaning easier, either manually or in-place. The unit opens within its own footprint simply by loosening the tie-rod bolts and rolling the movable frame back to the support column.
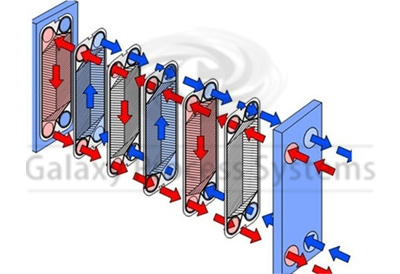